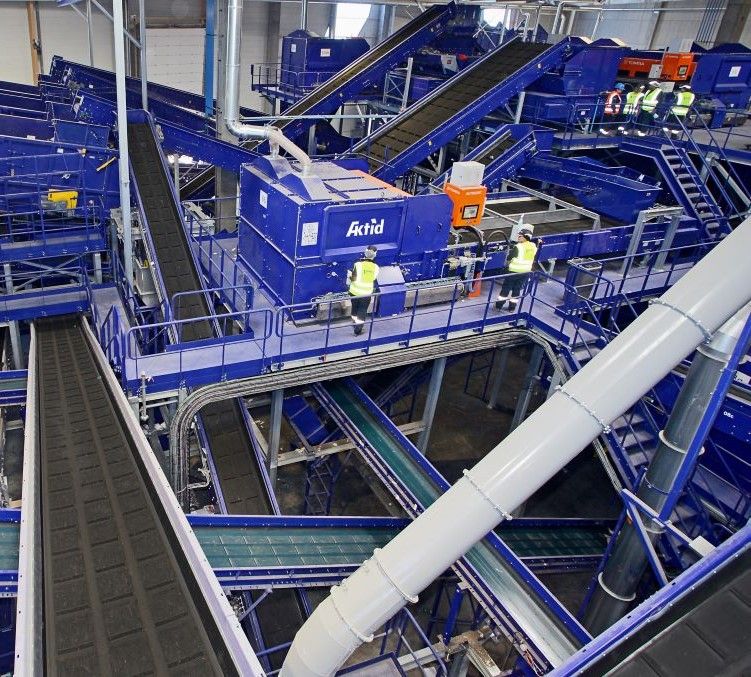
Aktid: Smart Solutions® per l’impianto Trivalo 69 a Chassieu
L’impianto realizzato da Aktid per il gruppo Paprec si configura come uno dei suoi progetti più ambiziosi, che ha dato vita a un centro di selezione ultramoderno.
Lo stabilimento Trivalo Rhône-Alpes (69) situato a Chassieu – Lione - è infatti uno dei più grandi in Francia in termini di capacità di selezione, arrivando a processare 60.000 tonnellate all’anno di raccolta differenziata. Utilizza le tecnologie più recenti per quanto riguarda l’automazione della selezione, distinguendosi per le sue caratteristiche in termini di portata, efficienza e purezza dei materiali in uscita.
Frutto di una partnership tra Aktid e Paprec, l’installazione presenta 11.900 metri quadri di attrezzature all’avanguardia integrate con intelligenza artificiale e Smart Solutions®, una gamma di prodotti studiati da Aktid per migliorare il funzionamento e le performance di selezione. L’obiettivo prefissato è infatti importante: il recupero del 98% dei prodotti valorizzabili grazie a 13 flussi. “Per raggiungere questi risultati ci siamo basati sulle nostre esperienze comuni strutturando la realizzazione dell’impianto su due assi principali: meccanizzazione avanzata in testa alla linea e notevole automazione dei processi di selezione” inizia Pierre-André Payerne, presidente di Aktid. “Abbiamo inoltre dotato l’impianto di nuovi sistemi di sicurezza e di ottimizzazione delle prestazioni sviluppati dai nostri team, che portano l’impianto di Paprec in una nuova era di industrializzazione della selezione” aggiunge.
Un processo complesso ed efficiente
L’impianto può trattare fino a 20 tonnellate all’ora grazie alle sue 184 macchine installate e ai 2.000 metri lineari di nastri trasportatori. Nel dettaglio, l’impianto è diviso in due linee: all’ingresso sono installate due tramogge dosatrici, di cui una dotata di aprisacco. Due separatori balistici sviluppati da Aktid, uno per ogni linea, fungono da decartonatori per separare i materiali di grandi dimensioni dal resto del flusso in modo da facilitare il lavoro degli operatori posizionati su quattro linee di preselezione. Il sottovaglio va ad altri tre separatori balistici che separano i corpi tridimensionali (bottiglie), i corpi fini e i corpi piatti (carta). Infatti, il movimento delle palette metalliche del vaglio agita il materiale che rimbalza seguendo una curva balistica: le bottiglie rotolano indietro, i corpi piatti procedono avanti e il materiale fine cade sotto.
Una buona preparazione meccanica del flusso in ingresso alla linea è una delle chiavi essenziali per il successo del processo di selezione. Per questo motivo da oltre 15 anni Aktid sviluppa i suoi separatori balistici che, grazie all’ampia superficie di vagliatura, al design specifico delle palette e al range di movimento, offrono un livello di separazione e flessibilità operativa senza eguali sul mercato. I materiali recuperabili passano alla successiva fase di selezione ottica: quindici macchine in totale, di cui nove per la cernita dei corpi piatti, quattro per i corpi tridimensionali e due per i film plastici. Con una larghezza di 2.800 mm, queste selezionatrici ottiche beneficiano delle dimensioni maggiori disponibili sul mercato.
Inoltre, una delle caratteristiche specifiche di questo impianto è l’integrazione di un robot di selezione. A differenza del principio della separazione ottica, il robot preleva i materiali recuperabili (acciaio, alluminio e bottiglie di plastica trasparente) sulla linea dello scarto poco prima di passare al controllo qualità effettuato da un unico operatore in cabina. Il robot esegue 65 movimenti al minuto, ovvero il 50% di movimenti in più rispetto a un operatore, su un nastro che va anche più veloce.
Ma per raggiungere delle prestazioni così elevate, l’efficientamento dei processi ha interessato l’intero sistema dell’impianto ottimizzandolo nel suo complesso. Seguendo lo stesso obiettivo, tutti i materiali fini vengono infatti trattati in tre vagli a dischi di varie dimensioni al fine di recuperare piccoli flaconi e altro alluminio frantumato per ottimizzare la valorizzazione delle frazioni.
Parola d’ordine: innovazione
Tra i punti di forza dell’impianto di Chassieu spicca il suo livello di automazione. Riuscire a raggiungere un tasso di recupero del 98% dei materiali valorizzabili, con una portata di 20 t/ora e un tasso di scarto così elevato, è un’impresa. La velocità di imballaggio dei prodotti selezionati è uno dei problemi più complessi da gestire su un impianto di questa tipologia. Opinione totalmente condivisa da Aktid che ha sviluppato Smart Packing, parte della gamma Aktid Smart Solutions®, il primo sistema di pressatura automatica sul mercato in grado di mettere più balle in fila.
“Alcuni impianti sono già dotati di presse automatiche ma nessuno, per quanto ne so, ha avuto successo fino ad ora nella produzione di treni di balle, soprattutto a un ritmo simile”, afferma Pierre-André Payerne. Quando uno dei silos, infatti, è pieno, l’informazione ritorna al sistema di gestione computerizzato che avvia automaticamente il processo di pressatura: i nastri e la pressa si avviano, il silo si svuota, la pressa produce da una a tre balle, il silo si chiude. Mentre la pressa sta ancora imballando, il ciclo successivo può ricominciare con l’apertura di un altro silo. Ogni silo è dotato di sensori che consentono l’imballatura automatica in base al proprio tasso di riempimento.
Inoltre, tutta l’installazione è controllata da un altro prodotto Smart Solutions®: ABI (Aktid Business Intelligence). Attraverso il suo dipartimento di ricerca e sviluppo, Aktid sta implementando da ormai diversi anni un software per la gestione delle prestazioni dei centri di selezione, che a Chassieu ha installato nella sua versione più completa. Pensato da e per gli operatori dei centri di selezione, l’obiettivo di ABI è quello di ottimizzare le prestazioni dell’impianto anticipando i potenziali guasti. Per ottenere ciò, il sistema analizza costantemente le operazioni, ne misura l’efficienza e reagisce alla minima deviazione di funzionamento. In questo caso le informazioni vengono inviate istantaneamente alla centrale dell’impianto, in modo che l’operatore possa reagire in maniera preventiva evitando possibili reazioni a catena. Il tasso di disponibilità dell’impianto risulta così ottimizzato.
“L’impianto di Chassieu è un altro traguardo importante per Aktid, che ha messo in evidenza ancora una volta la sua competenza in materia di innovazione, l’affidabilità nelle soluzioni proposte e il suo approccio centrato sulle esigenze del cliente. Aktid si distingue così come realtà di riferimento nello sviluppo dei centri di selezione rifiuti di domani” afferma Marco Crociani, CEO di Aktid Italia.