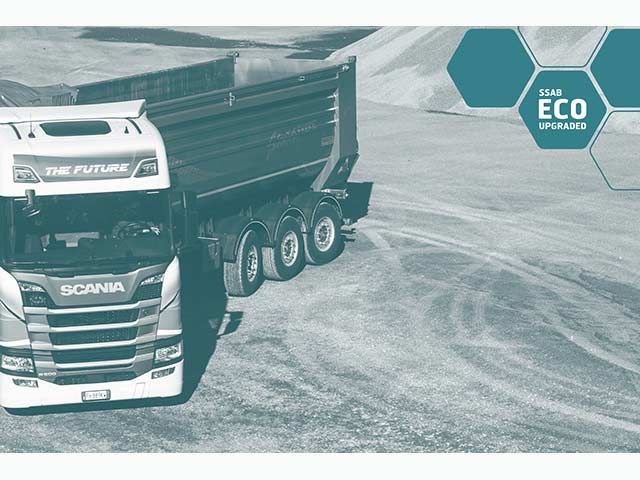
Taking a load off the environment with SSAB EcoUpgraded
Building muscle – while staying lean, mean and green.
When customers upgrade from standard steel to high-strength steel, they can cut the weight of the end product while maintaining the same strength and increasing durability and productivity. From a lifecycle perspective, this is crucial because most of the negative environmental impact comes from a product’s use phase.
And because high-strength steel is stronger than conventional mild steel, less steel is needed to manufacture the product. This also reduces CO2 emissions. An SSAB EcoUpgraded product will generate CO2 savings that exceed the CO2 emitted during the production of the upgraded part. The amount of the savings varies depending on the design and whether or not it is weight-critical.
SSAB looks at each specific application and compares the potential CO2 savings in the use phase to the CO2 emitted during production. This way, we identify products that would benefit the most from an upgrade to high-strength Strenx® performance steel and/or Hardox® wear plate. Once the CO2 payback time is reached, the vehicle will continue to deliver CO2 savings far in excess of the original CO2 debt.
Rock-solid benefits
Here’s how high-strength steels from SSAB benefit both the environment and our customers’ businesses.
- Thinner dimensions of steel can be used without compromising on strength
- Fewer resources used in the manufacture of SSAB EcoUpgraded components and vehicles
- Less fuel needed for the same work – haul the same load in fewer number of trips
- Lower carbon dioxide emissions over entire lifecycle
- Meet and stay ahead of tougher environmental requirements and legislation
- OEMs can enhance their environmental profile and gain a competitive edge
From good to great: A customer success story
Successful projects and satisfied customers bear witness to the success of EcoUpgraded on many levels. For one customer, an ultra-light tipper chassis used 610 kg of Strenx® 960MC Plus to replace 750 kg of S700MC steel. And in the body, 830 kg of Hardox® 500 Tuf replaced 1,000 kg of Hardox® 450.
This brought a total weight reduction of 18% for the upgraded parts. The body’s lifetime was doubled, to 12 years, eliminating the need to change the body on this chassis. And the weight was reduced by 310 kg, which increased the load capacity by the same amount.