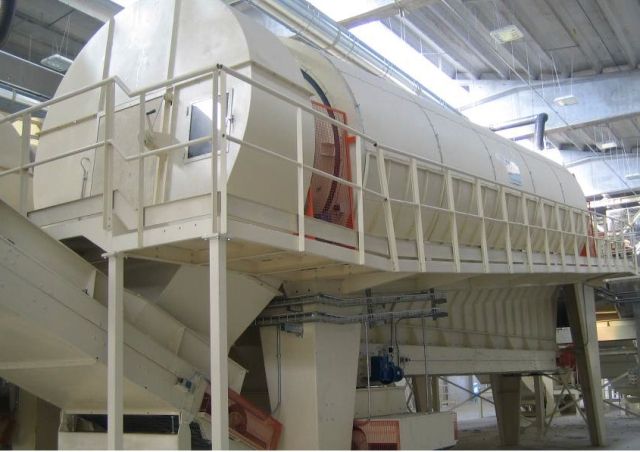
Amut and Amut Ecotech joint players to supply recycling facilities
The Italian Amut Group is globally considered as synonymous of flexibility and turn-key solutions mainly because all of its divisions and companies collaborate together, sharing knowledge and professional competences in three sectors: extrusion, thermoforming and recycling.
As a result of this strategy, Amut Group is always in position to supply tailor-made equipment and installations to satisfy a wide range of requirements. Amut Recycling Division, innovative manufacturer of plastics washing plants, together with Amut Ecotech, high expert of sorting and separation technology, represent an instrumental player in the waste processing systems field. Amut and Amut Ecotech become a sole reference to supply recycling facilities.
Confirming this important strength, a recycling plant has been recently supplied in England for a customer who preferred Amut over the others, not only for technological reasons but also because he could find the advantage to buy a turn-key mixed plastic sorting plant and HDPE washing plant by an unique supplier.
In fact, Amut plant is able to cover the comprehensive recycling flow from mixed plastics sorting up to the delivery of flakes. These flakes have a quality level suitable to be re-used in further extrusion, injection or thermoforming process. The plant reclaims polyolefin thermoplastics scraps to be transformed into granules with an output of 10 Tons/h.
The thermoplastic scraps come from the urban and industrial separate collection and they
are previously selected as:
- HDPE / PP containers and bottles for foods.
- HDPE / PP containers and bottles for detergents and chemicals.
Plastics at inlet: HDPE and PP (75%), heavy plastics (25%).
Amut designers usually work in collaboration with the technicians joining their efforts to develop performing machines and proper structure in terms of optimisation of the overall dimensions and of an easy handling to facilitate the maintenance interventions.
Amut Ecotech - PRF
The plant is fed by mixed plastics materials packed into bales, loaded by a forklift on the extracting chain conveyor installed in a pit, weighing system equipped with, and then conveyed to the “bales breaker machine”, properly designed and manufactured to break up bales mainly composed by plastic materials. This machine doesn’t shred material but gets back bulk material in order to feed the recovery plant in a constant and regular way. Breaking up of the bales is assured by the circular motion of a drum equipped with fix teeth. The rotor’s sharp tools enter the bales separating in this way all materials that fall in the below conveyor belt, conveying materials to the pre-sorting picking cabin where pickers take way bulky materials, mainly represented by cardboard and film, from the stream. After this first selection, by a feeding conveyor, the material flow is conveyed in the rotary trommel, where the separation depends on size. Three different streams are possible.
1. Material having size smaller than 30 mm falls on a conveyor belt, where is conveyed, jointly to the one fine coming from the ballistic separators, to the residue storing unit.
2. Material having size between 30 and 260 mm, is conveyed to the ballistic separator where the rolling shape and the hard materials are separated from the light and flat ones by the paddles sussultory movement. Furthermore, thanks to the grids installed on the paddles, fine material not yet separated by the rotary trommel, is evacuated and conveyed to the special storing unit. Flat and light material are conveyed upward by a conveyor.
“Rolling shape and hard materials” sorted by the action of the ballistic separator, are conveyed to the plastics automatic selection line where plastic material will be automatically selected by optical readers.
3. Oversize materials stream, having size bigger than 260 mm is conveyed to the bulky materials picking line, where, different types of materials, mainly film and good plastics to be sent to the automatic line are manually selected and discharged in chutes.
In order to get the higher quality of materials, after the NIR optical reader they are provided QC (quality control) stations, where pickers recycle errors, conveyed at the beginning of the automatic line to get more efficient the line. A manual checking line is also provided.
Before entering the automatic line, “rolling shape and hard material” (plastic materials stream) stream passes through a de-metallization line, consisting of an over band magnetic separator used for ferrous materials and, an Eddy Current System (based on the Foucaults currents principle), used for no-ferrous metals. Ferrous and no-ferrous materials selected in the de-metallization line, are weighed by weighing system hopper and then discharged into hook-lift containers.
Amut – Washing System
The main washing action on the product is made by the Friction Washer, thanks to the intensive friction of the rotary paddles among the flakes. Even if it is continuously fed, the friction washer allows an adjustment of the stay time of the material.
A characteristic of this unit is its noiselessness, therefore a soundproof box is not required. The water, coming from the friction washer with paper pollutants, is filtered and then used again for the process.
After this strong washing action, the rinsing cycle starts into two proper troughs in series where there is also the separation of light pollutants (paper, non-polyolefin thermoplastics, etc.). The material is introduced in the bottom of the rinsing troughs in order to improve their efficiency.
The light pollutants are so decanted, while the polyolefin float. Also these rinsing troughs are equipped with an automatic extractor of decanted material and heavy plastics. This mixed plastics are dried by a centrifuge and stored in big bags. The Washing Section operates in a fully automatic cycle, controlled by a centralized board.
The equipment has been designed to assure both separation and complete cleaning of thermoplastic material from all the pollutants having specific weight higher than the thermoplastics one.
Possible residuals of pollutants, not extracted in the Washing Section, will be filtered during the process in the Granulation Section. Once all materials are selected, they are stored into the storing unit by type, ready to be discharged in the collecting conveyors to be then sent to the baling press, for the final packaging of bales.